Essential rigid pipe threader machine you need to Have
A pipe grooving machine is a tool that is used to create grooves or indentations at the end of a pipe. These grooves are then used to connect the pipes together using couplings or fittings. Pipe grooving machines are commonly used in the construction industry to install fire sprinkler systems and other piping systems.
The pipe grooving process involves feeding the end of the pipe into the machine, where it is then clamped in place. The machine then rotates the pipe while a grooving wheel is pressed against the end of the pipe, creating the groove. The depth and width of the groove can be adjusted depending on the size of the pipe and the type of coupling or fitting that will be used.
Pipe grooving machines can be either manual or automatic, with automatic machines being more efficient and precise. They are available in various sizes and configurations, with some models being portable for use in remote locations.
There are many advantages to using pipe grooving machines. Firstly, they are fast and efficient, allowing for the grooving of a large number of pipes in a short amount of time. Secondly, they produce precise grooves that are uniform in size and depth, ensuring a secure connection between the pipes. Additionally, grooved pipes are more flexible than threaded pipes, reducing pipe stress and preventing leaks.
In conclusion, pipe grooving machines are an important tool in the construction industry for creating secure connections between pipes. They are fast, and efficient, and produce precise grooves that are essential for properly installing piping systems.
A pipe-cutting machine is an industrial tool used to cut various types of pipes with precision and accuracy. Pipe-cutting machines can be used for cutting pipes made from different materials such as steel, copper, aluminum, and plastic. These machines are commonly used in the construction industry, plumbing, and various manufacturing processes where pipes need to be cut to specific lengths.
Pipe-cutting machines are available in different sizes and types, including manual, semi-automatic, and fully automatic machines. Manual pipe-cutting machines require an operator to manually adjust the cutting blade and feed the pipe through the machine. Semi-automatic machines have some automated features, such as automatic clamping and blade rotation. Fully automatic machines have advanced automation features that can cut pipes without any human intervention.
Pipe-cutting machines use different cutting methods, including abrasive cutting, cold cutting, and flame cutting. Abrasive cutting involves using an abrasive blade to cut through the pipe, while cold cutting uses a saw blade to cut through the pipe. Flame cutting involves using a high-temperature flame to cut through the pipe.
The benefits of using a pipe-cutting machine include increased accuracy, speed, and efficiency. These machines can cut pipes to precise measurements, ensuring that they fit together perfectly. They can also cut multiple pipes at once, which saves time and increases productivity. Additionally, pipe-cutting machines can cut pipes quickly and cleanly, reducing waste and ensuring a smooth edge on the pipe.
In conclusion, pipe-cutting machines are essential tools for the construction industry, plumbing, and various manufacturing processes. They offer precision, accuracy, speed, and efficiency in cutting different types of pipes to specific lengths. The different types and sizes of pipe-cutting machines available make them suitable for various applications, and the cutting methods used allow for different materials to be cut with ease.
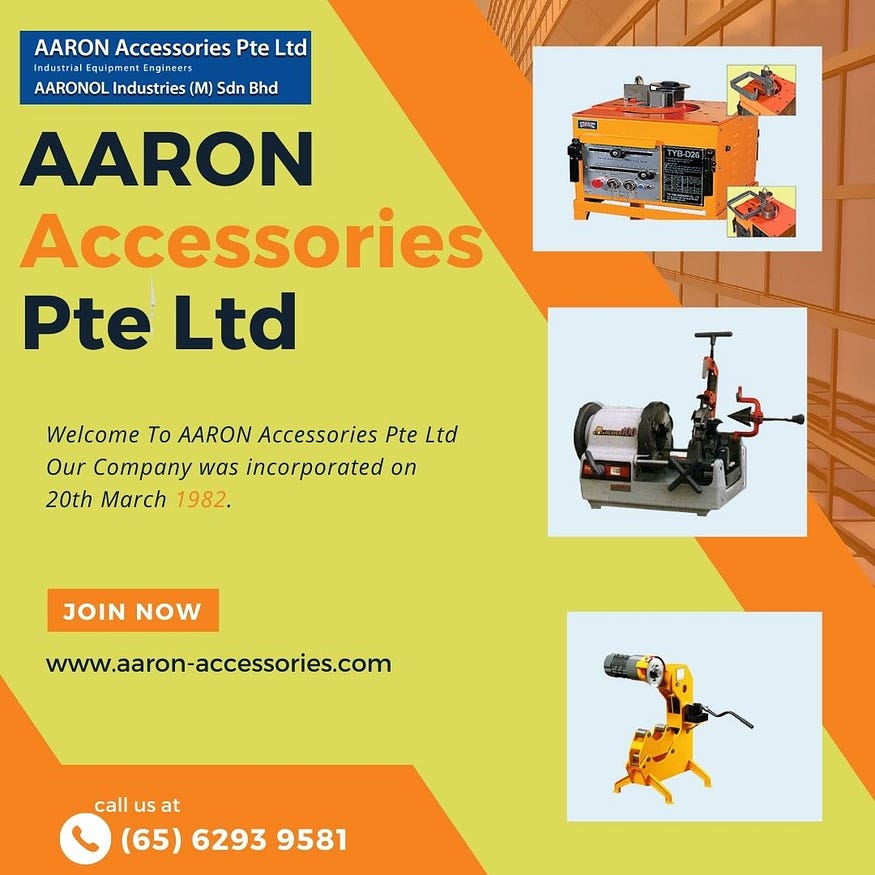
A pipe threading machine is a tool used to thread the ends of pipes, allowing them to be screwed together to form a secure connection. These machines are commonly used in the plumbing and construction industries for installing pipes and fittings.
Pipe threading machines come in different sizes and types, from handheld manual machines to large industrial al machines. Manual machines require an operator to adjust the cutting die and feed the pipe through the machine, while automatic machines have advanced automation features that can thread pipes without any human intervention.
The threading process involves clamping the pipe into the threading machine and rotating it while a cutting die is applied to the end of the pipe. The die cuts grooves into the pipe, creating threads that match the threads on the fittings or couplings. The depth and pitch of the threads can be adjusted depending on the size of the pipe and the type of fitting to be used.
The benefits of using a pipe threading machine include increased efficiency, accuracy, and consistency. Pipe threads created with a threading machine are precise, ensuring a tight and secure fit with the fittings or couplings. The machines can thread pipes quickly and consistently, allowing for a high volume of pipes to be threaded in a short amount of time.
In addition to threading pipes, some pipe threading machines can also cut and ream pipes, making them versatile tools for the construction and plumbing industries. By having a machine that can perform multiple tasks, eliminates the need for multiple machines and increases productivity.
In conclusion, pipe threading machines are essential tools for the plumbing and construction industries. They allow for the precise and efficient creation of threads on the ends of pipes, ensuring a secure and tight fit with fittings or couplings. With the different types and sizes of machines available, there is a machine suitable for various applications, making them a valuable investment for any plumbing or construction business.
0 Comments